The capacitance of a capacitor is determined by the dielectric material that separates its plates. This property, along with its temperature stability and ESR (equivalent series resistance), determines its suitability for a specific application. Capacitors can be found in a wide variety of devices, from the miniaturized MLCCs used in smartphones and cars to large film power capacitors critical for energy-saving systems such as uninterruptible power supplies and frequency converters.
Aluminum electrolytic capacitors remain at the core of the industry, offering a wide range of case sizes and capacitance values for designers who are limited by space or mission-critical applications. They are available in a broad selection of technologies, including dry and wet aluminum oxide and amorphous silicon dioxide, and can also be rated for different temperatures.
While many aluminum electrolytic capacitors are still produced in a can, smaller, more compact versions have also become popular in digital devices such as tablet PCs and flat panel displays. These capacitors have a much smaller footprint than traditional can-type aluminum electrolytic capacitors, yet maintain the high performance characteristics required in these new applications.
The ability to withstand high voltages and fast pulses is an important requirement for any capacitor used in electronic circuitry. These requirements are reflected in the voltage rating of the capacitor and are known as its surge capability. A capacitor’s surge capability refers to the value of the capacitor that can be applied for a short period of time at a specified temperature and without damage to the dielectric or an increase in the equivalent series resistance (ESR) that could significantly reduce its useful life span.
To ensure the safety of devices that use
aluminum electrolytic capacitors, manufacturers have developed a wide range of test standards. These tests help engineers and QA professionals evaluate the quality of these components and identify any potential problems before they are used in their final products. For example, a common test involves applying a brief surge to a capacitor and measuring the current flow through it. This is called a burst testing method and is designed to detect defects that would otherwise be invisible to the naked eye.
A capacitor’s peak voltage is another important factor to consider when selecting a component. This is typically measured under a specific temperature and time condition, such as a 1,000-cycle cyclic test at 125 degC with 30 seconds of dwell and 5 minutes of pause. The surge capability of a capacitor is determined by the amount of voltage that can be sustained for 30 seconds at the specified temperature, without visible damage to the capacitor or a significant increase in its ESR.
Other factors that affect a capacitor’s performance include its leakage current, its temperature stability, and its size and form factor. The leakage current is a DC current that flows through the capacitor when it is not being charged or discharged, and it influences both the capacitance and impedance of the device. Temperature stability is an important factor because the liquid electrolyte in an aluminum electrolytic capacitor evaporates over time.
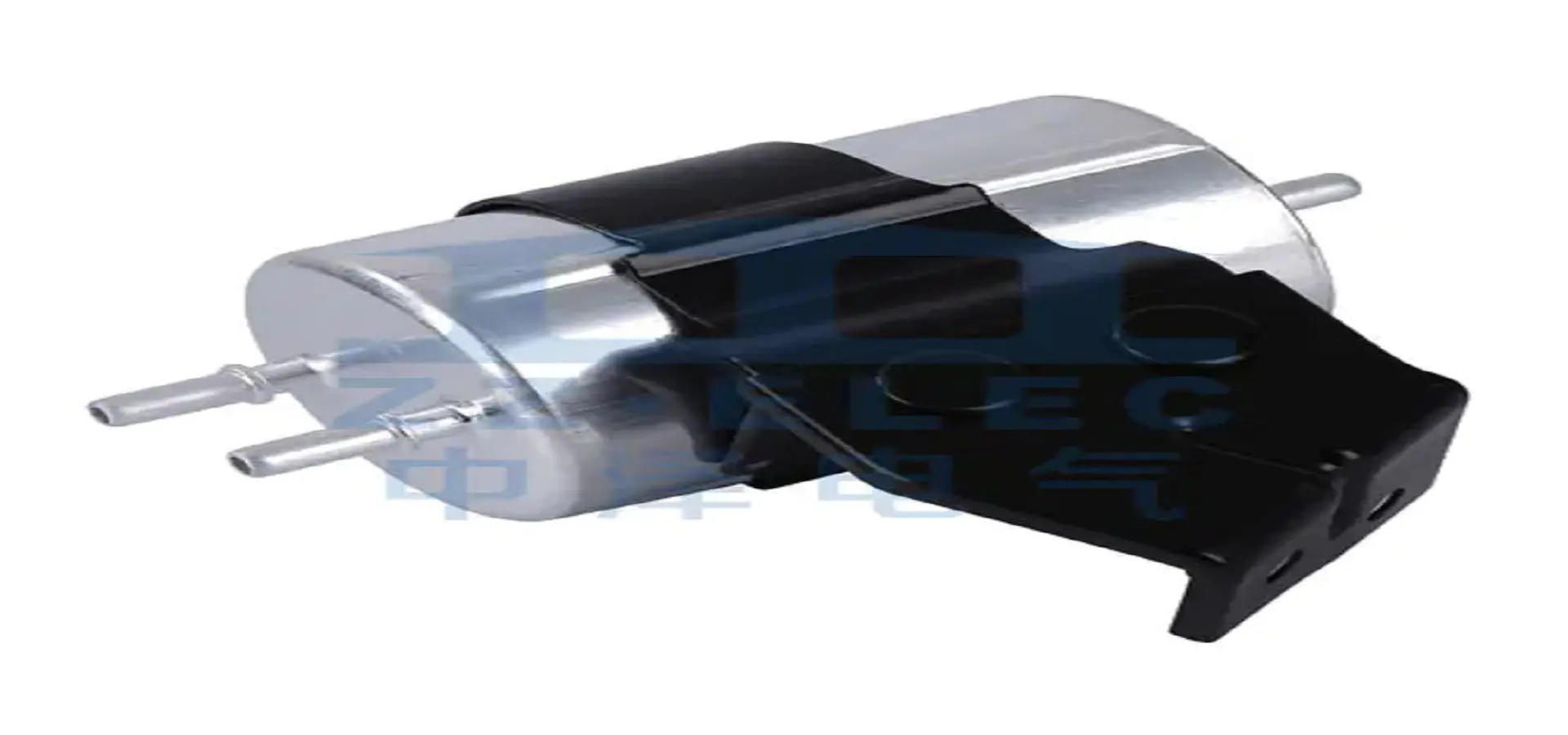