Aluminum
electrolytic capacitor components Factory produce a wide range of metallized film capacitors. They are used in electronic devices for smoothing and buffering rectified DC voltages, especially in switched-mode power supplies. They also serve as DC link capacitors in drives and frequency converters for photovoltaic, wind power and industrial applications. The capacitance values are highly dependent on the type of dielectric. The amorphous variety (sometimes also called metallized amorphous oxide) is less sensitive to mechanical stress than the crystalline type and has a lower leakage current. The capacitors are polarized, and they can only be operated with the correct DC voltage applied to the anode and cathode foils. Operating the capacitor with the wrong polarity will damage or destroy it.
The capacitor is made of an aluminum cylinder as the negative electrode, filled with liquid electrolyte and inserted into a bent aluminium strip as the positive electrode. The negative electrode is etched or roughened in order to increase the surface area and to make contact with the electrolyte. A paper spacer mechanically separates the anode and cathode aluminum foils to avoid direct metallic contacts. The etched and roughened anode foil is then covered with a layer of oxidized aluminum oxide. The oxidized layer acts as the dielectric of the capacitor and is structured by a chemical treatment to either amorphous or crystalline aluminum oxide.
The amorphous oxide has a better performance than the crystalline variety, with a higher dielectric ratio and a lower leakage current. The amorphous oxide layer is also less sensitive to tensile stresses. The crystalline aluminum oxide is more susceptible to cracking when subjected to mechanical stress, like during the cutting and winding of the element, or to thermal stress, like during the post-forming process.
Another factor which influences the capacitance value of the capacitor is the internal resistance, or ESR (Equivalent Series Resistance), caused by the metal electrodes and the electrolyte. The ESR can be influenced by the structure of the anode foil, the thickness of the oxide layer, the spacer paper and the position and winding alignment of the elements. The ESR can be reduced by a special manufacturing process, but it cannot be eliminated completely.
Generally, the aluminum electrolytic capacitor has a high ESR at low frequencies. However, the ESR drops significantly as the frequency rises, mainly due to the fact that the aluminum cylinder becomes a heat sink and dissipates the generated internal heat. This characteristic makes the capacitors ideal for use at medium and high frequencies, up to mains frequency. The high ESR of the aluminum electrolytic capacitors means that they must be protected from overvoltage, or transient overvoltages, as these are able to damage or even destroy them. Hence, the manufacturers of these types of capacitors must ensure that their products are tested for overvoltage tolerance in a special laboratory test and provide an overvoltage tolerance specification. This test, known as the surge voltage test, defines a short time period within which the capacitor can be subjected to an overvoltage of a certain level without causing any visible damage or a change in capacitance value greater than 15%.
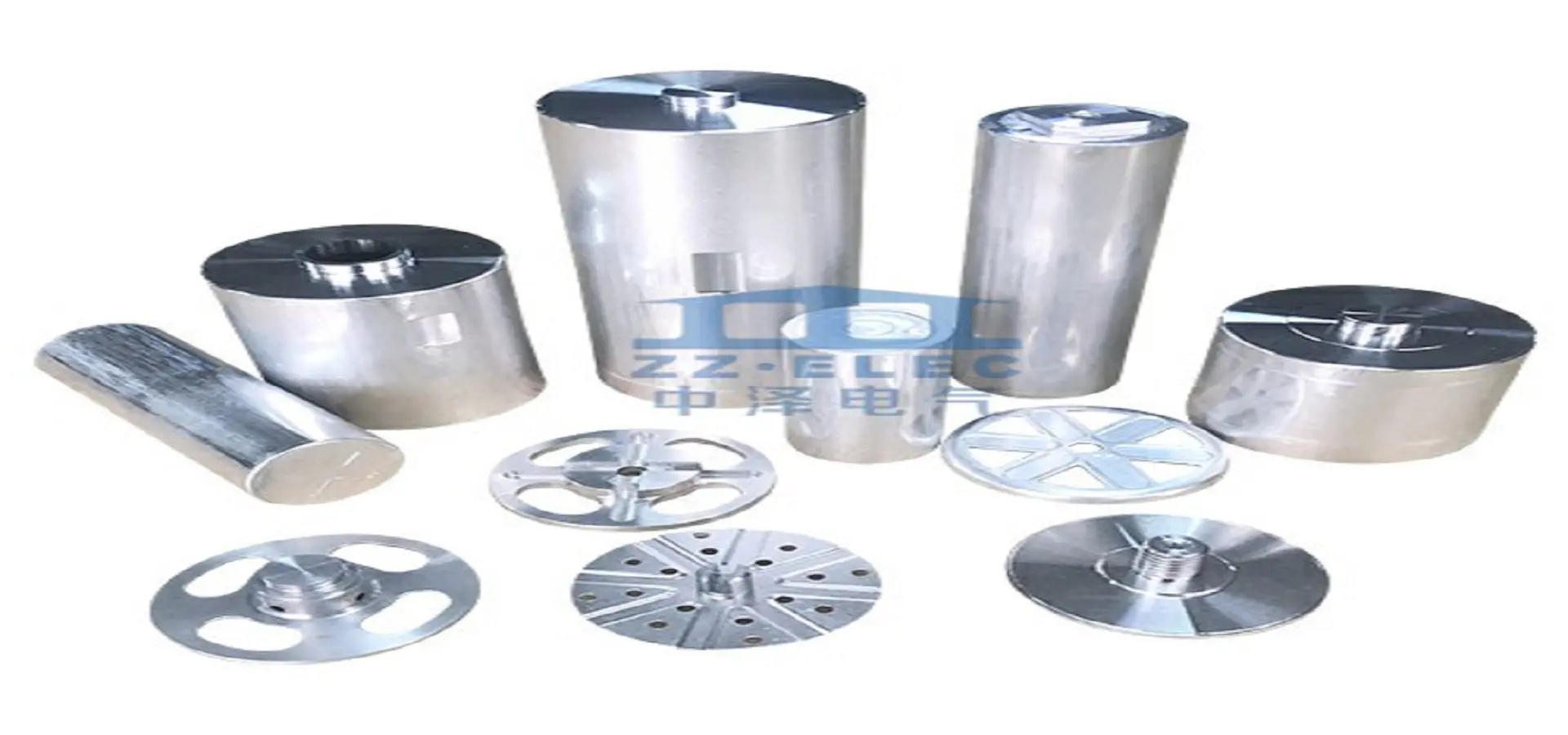