Aluminum Cold extrusion is one of the processes that produces high-quality aluminum products. This process is characterized by the lack of heating during the process, making it a good choice for parts where strength and malleability are important. During cold extrusion, the billet is fed through a series of molds to achieve a specific shape and thickness. After the process is completed, the billet is ready for post-processing.
Aluminum extrusion processes start with a billet or log, which can be circular or square. The billet is produced by mixing pure aluminum and other metals to create an alloy. This alloy is then melted to remove impurities and is then poured into a form. After that, it is under high pressure to expel air, leaving a solid block of aluminum.
The process is characterized by the use of dies and metal tools. The dies, which are thick circular disks with openings, are made of steel and are heat-treated to withstand the high pressure of the hot metal.
The raw aluminum is pushed through the dies at a pressure of between 100,000 and 125,000 psi. The dies used in extrusion processes come in several types. There are solid dies that produce shapes without any openings in the center, hollow dies with one or multiple openings, and semi-hollow dies, which are al hollow.
Aluminium cold extrusion is especially useful for cases where the diameter/length ratio is important. In addition, it can produce interesting shapes and internal integrated pipes. The advantages of cold extrusion include increased production speed, lower costs, and improved mechanical properties. Aluminium Cold extrusion is typically combined with other processes to enhance its efficiency and quality.
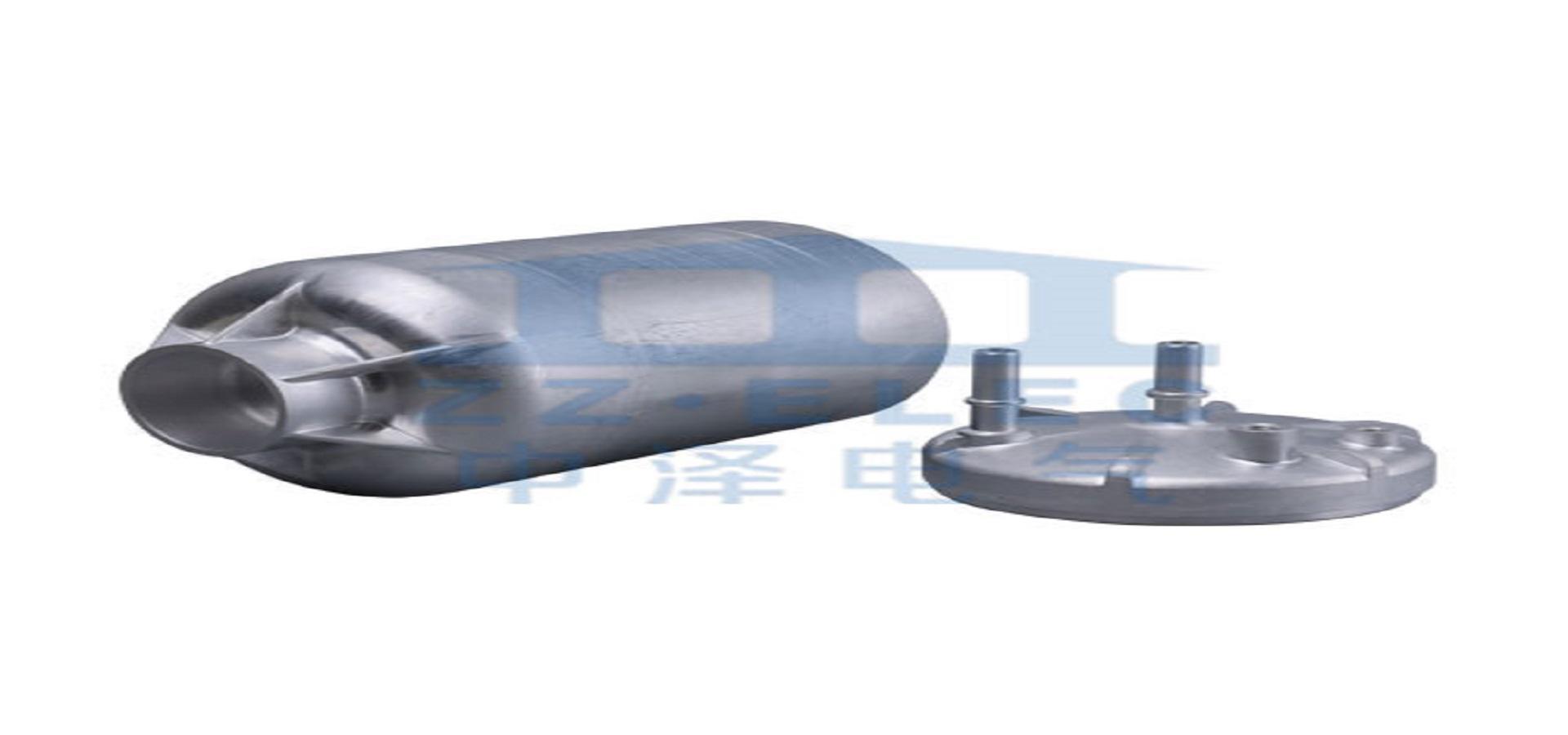