Benefits of Aluminum Cold Extrusions:
1. Material Strength and Integrity:
One of the key benefits of aluminum cold extrusions is the enhancement of material strength and integrity. The extrusion process aligns the grain structure of the aluminum, resulting in improved mechanical properties such as tensile strength and hardness. This s to stronger and more durable components, ensuring their longevity and reliability in various applications.
2. Complex Geometries and Design Flexibility:
Aluminum cold extrusions allow for the creation of intricate and complex shapes with high dimensional accuracy. The flexibility of the extrusion process enables the production of customized profiles and components, accommodating the specific design requirements of various industries. This design versatility opens up opportunities for innovative and efficient product designs that were previously challenging to achieve with traditional manufacturing methods.
3. Waste Reduction and Material Efficiency:
Cold extrusion of aluminum offers high material efficiency and minimal waste generation. The process utilizes the aluminum material effectively, resulting in minimal material loss during production. Additionally, the ability to extrude complex shapes reduces the need for additional machining operations, minimizing material waste and overall production costs.
4. Cost-Effectiveness and Efficiency:
Aluminum cold extrusions offer cost-effective manufacturing solutions. The process allows for high-speed production with shorter cycle times, contributing to efficient production rates and reduced labor costs. Furthermore, the elimination or reduction of secondary operations, such as machining or welding, s to lower production costs and improved overall efficiency.
5. Surface Finish and Aesthetic Appeal:
Cold extruded aluminum components exhibit surface finish and aesthetic appeal. The extrusion process produces smooth and uniform surfaces, eliminating the need for additional finishing operations. This results in visually appealing products with consistent quality, making them suitable for applications where aesthetics play a significant role, such as architectural elements, automotive trim, and consumer goods.
Applications of Aluminum Cold Extrusions:
1. Automotive Industry:
Aluminum cold extrusions find extensive applications in the automotive industry. The lightweight nature of aluminum combined with the ability to create complex profiles makes cold extrusions ideal for automotive components such as heat sinks, engine parts, structural elements, and suspension components. These extruded aluminum parts contribute to weight reduction, fuel efficiency, and improved vehicle performance.
2. Aerospace and Aviation:
The aerospace and aviation sectors also benefit from aluminum cold extrusions. The high strength-to-weight ratio of aluminum components produced through cold extrusion makes them suitable for aircraft structural elements, aerospace frames, engine components, and interior fittings. The lightweight nature of aluminum contributes to fuel efficiency, while the durability ensures the safety and reliability of aerospace systems.
3. Building and Construction:
Aluminum cold extrusions are extensively used in the building and construction industry. The ability to extrude complex profiles allows for the production of aluminum architectural elements, window frames, curtain walls, and structural components. The lightweight nature of aluminum simplifies installation, reduces structural loads, and offers design flexibility in architectural applications.
4. Electrical and Electronics:
The electrical and electronics industry benefits from aluminum cold extrusions for the production of heat sinks, enclosures, and electronic component housings. The enhanced thermal conductivity of aluminum, coupled with the ability to create intricate heat sink designs through extrusion, ensures efficient heat dissipation and performance of electronic systems.
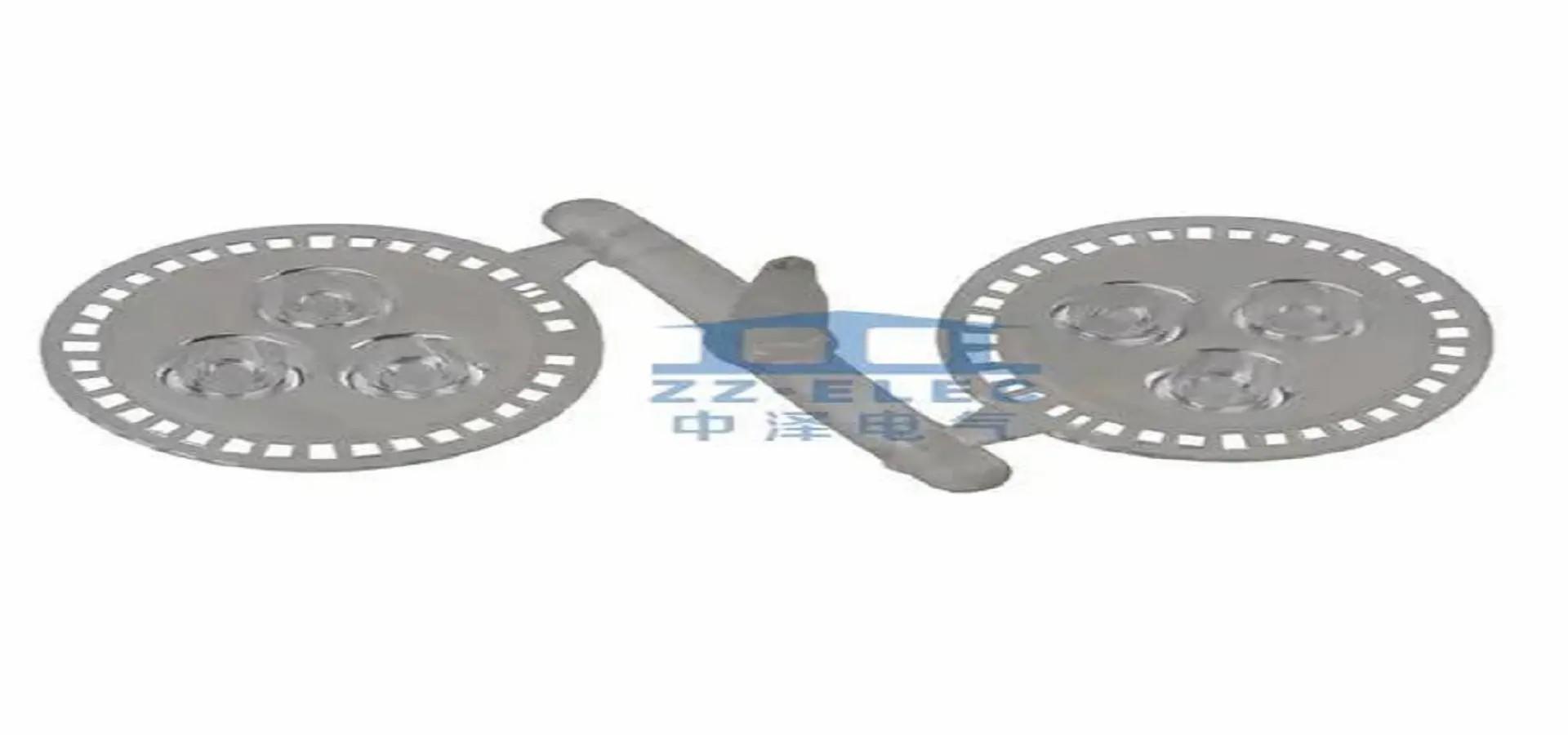