Aluminium cold extrusion is a versatile manufacturing process that plays a pivotal role in shaping the modern world. This technique involves forcing aluminum through a die at room temperature, creating complex shapes and precise components. The process harnesses the malleability of aluminum, offering numerous advantages in terms of cost-effectiveness, efficiency, and sustainability.
Cold extrusion results in mechanical properties for aluminum components. The process aligns the grain structure of the metal, enhancing its strength and durability. This makes cold extruded aluminum parts ideal for applications requiring high structural integrity.
Compared to hot extrusion, cold extrusion is a more cost-effective method. The absence of the high temperatures required in hot extrusion reduces energy consumption and eliminates the need for extensive cooling processes, contributing to overall cost savings.
Aluminium cold extrusion allows for the production of intricate and complex shapes with tight tolerances. This makes it suitable for manufacturing components such as automotive parts, aerospace components, and intricate structural elements.
Cold extrusion produces components with a smoother surface finish, reducing the need for additional machining or finishing processes. This not only saves time but also enhances the aesthetic appeal of the final product.
The automotive industry extensively relies on aluminium cold extrusion for the production of various components, including piston rods, transmission shafts, and structural elements. The lightweight yet sturdy nature of cold extruded aluminum contributes to fuel efficiency and overall vehicle performance.
Aluminium's combination of strength and lightness makes it an ideal material for aerospace applications. Cold extrusion is employed to manufacture critical components like aircraft fuselage sections, wing structures, and precision parts.
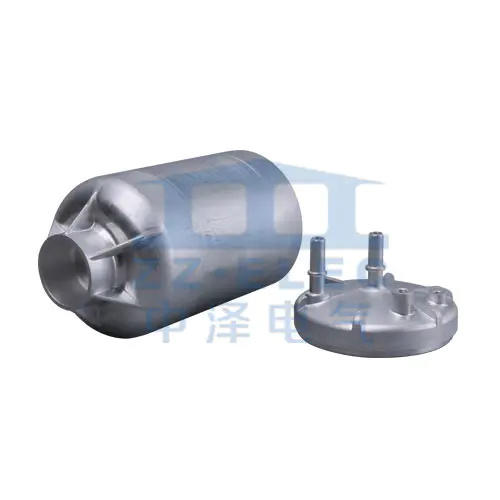