Electrolytic capacitors are a kind of component that is difficult to control the quality of the electronic industry. There are many product quality problems caused by electrolytic capacitors. Many manufacturers do not know how to check the quality of electrolytic capacitors and have to spend high prices to buy brand-name electrolytic capacitors. a lot of cost.
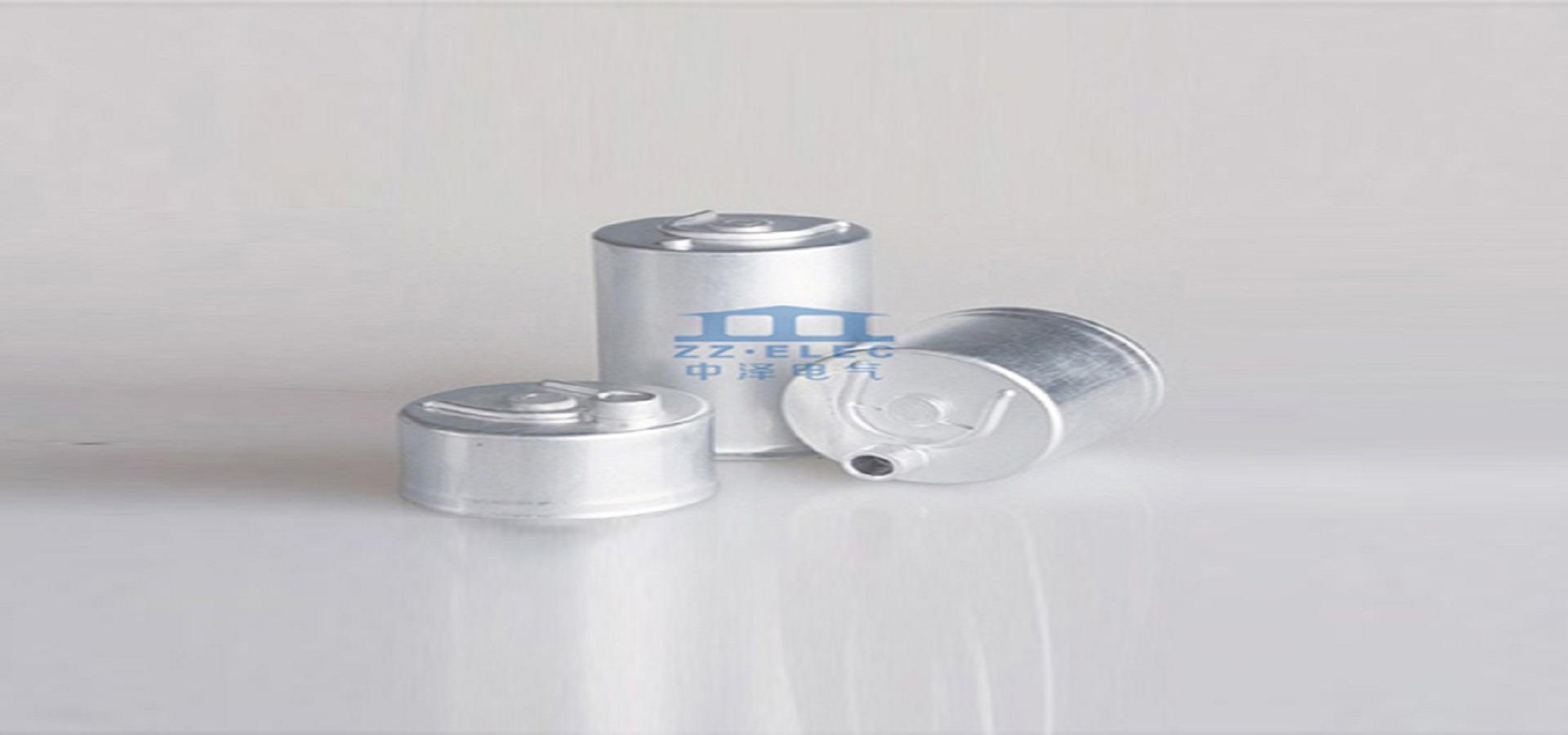
1. Principle: The main problem of electrolytic capacitors used in electronic ballasts is insufficient to withstand voltage or poor temperature coefficient during operation, resulting in damage to electrolytic capacitors. This method is to test the quality of the electrolytic capacitor by charging and discharging under the condition of the working voltage of the electrolytic capacitor. It is better to do screening at high temperatures if conditions permit. If the performance of the electrolytic capacitor is not enough, when there is a little leakage, the charge stored by other electrolytic capacitors will be released through the capacitor, resulting in the poor performance of the capacitor being blown up. Good-performance electrolytic capacitors are intact.
2. Selection of main components: T1 uses a 0-250V/1KW self-coupling voltage regulator, T2 needs to be customized, and the parameters are 500W, 220/380V step-up isolation transformer. DC voltmeter with 1000V range. S1 and S2 are linked switches, preferably the emergency brake switch on the machine tool can be used instead. A normal incandescent light bulb will do. The fuse is the delay fuse on the color TV.
3. Manufacturing method: First make a fixture, that can fix the pins of many electrolytic capacitors to be tested, and can be electrically connected reliably. Use another box to install everything in the box. The voltmeter, light bulb, switch, and voltage-regulating handle are installed on the outer surface of the box. After connecting the electrical circuit, the electrolytic capacitor can be screened.
4. Instrument debugging method: adjust the working voltage according to the requirements of the electrolytic capacitor, install the electrolytic capacitor on the fixture and clamp it, close the cover of the box, and press the power switch. At this time, the light bulb lights up and the pointer of the voltmeter is rising. , indicating that the circuit is charging the electrolytic capacitor, and when the specified voltage is reached, the light bulb goes out. Rotate the switch again, let the switch jump, then the light bulb lights up, indicating that the electrolytic capacitor is discharging, and the pointer of the voltmeter is falling. This indicates that the instrument is working properly.
5. Selection method of rated working voltage: In general, the rated working voltage is selected as 110-120% of the identification voltage of the electrolytic capacitor. If the identification voltage is 400V, then the working voltage is selected between 440-480V. For example, the instrument is selected as 440V in the case of high temperature, and 480V in the case of low temperature. Screening operation method: adjust the working voltage according to the identification of the electrolytic capacitor, turn off the power switch, install the electrolytic capacitor, clamp it, and cover the box cover. Turn on the power switch, turn it off, repeat three times, turn on the power switch again, hold for half an hour, repeat the switch three times, and finally turn off the power switch, take out the electrolytic capacitor, and this step of screening is completed. Note: If the electrolytic capacitors exploded, ruptured, or leaked during the test, they are all unqualified products, and others can be used as qualified products. A comprehensive screening method also includes the detection of capacitance, leakage current, and loss angle.