How to prevent cracks in the production process of SMD electrolytic capacitors? First, the process and production personnel must be informed of the thermal failure of the
chip capacitors, so that they can attach great importance to this problem. Secondly, they must be welded by specialized skilled workers and strict requirements on the welding process. For example, the soldering iron must not exceed 315° with a constant temperature soldering iron. C (To prevent the production workers from increasing the soldering temperature quickly), the soldering time should not exceed 3 seconds. Choose a suitable flux and solder paste, and clean the pad to prevent the MLCC from being subjected to large external forces.
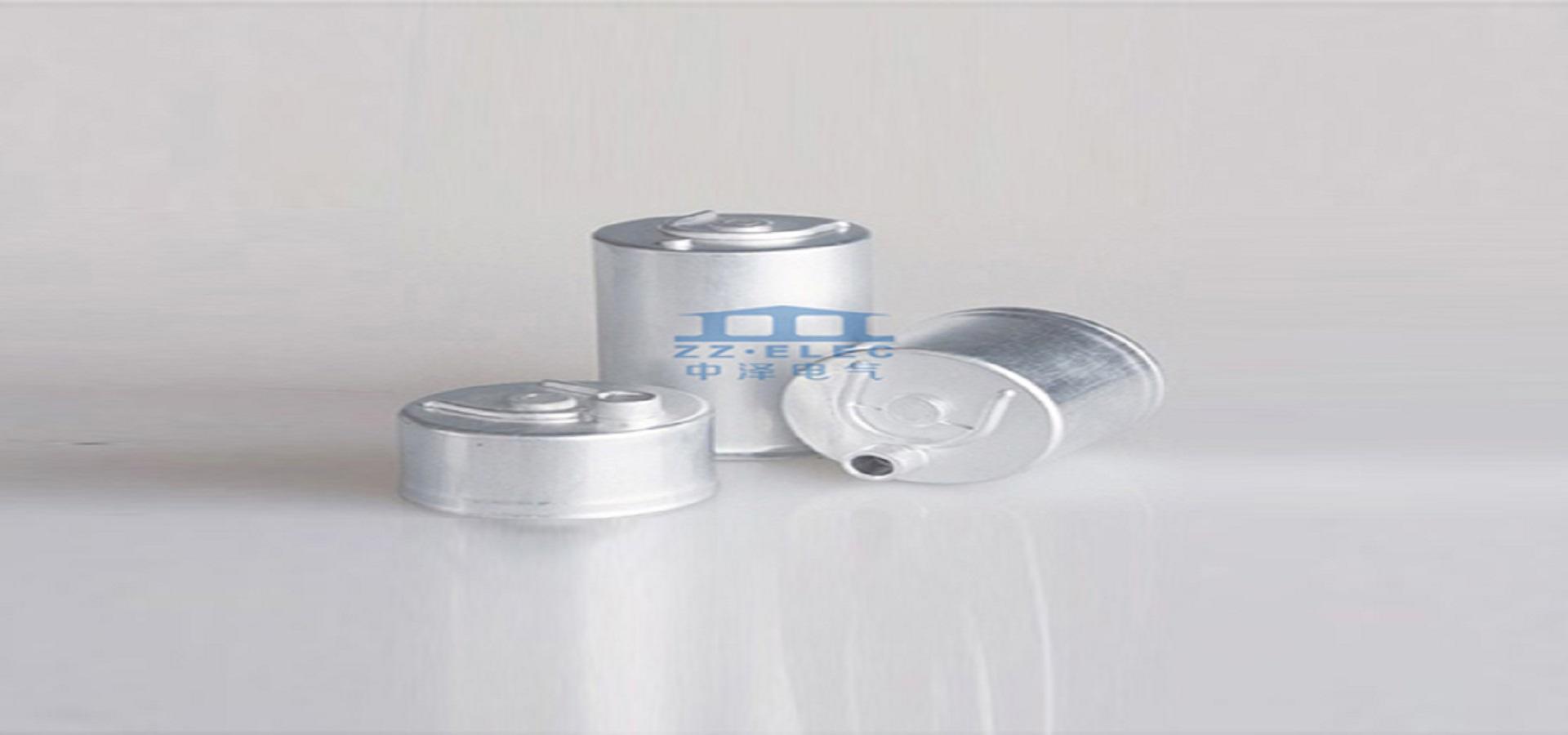
Pay attention to the quality of soldering, etc. The manual soldering is to put tin on the pad , then the soldering iron melts the tin on the pad and then put the capacitor on the soldering iron. The soldering iron only touches the pad and does not touch the chip capacitor during the whole process. It can be moved closer, and then use a similar method to heat the tin-plated underlayer on the pad instead of directly heating the chip capacitor, and soldering the other end.
Mechanical stress is also easy to cause cracks in the chip capacitors. Because the chip capacitors are rectangular (the surface parallel to the PCB), and the short side is the solder end, naturally the long side is prone to problems when subjected to force, so it is necessary to arrange the board. Consider the relationship between the direction of force, such as the direction of deformation when dividing the board, and the direction of the chip capacitor. In the production process, try not to place chip capacitors wherever the PCB may have a large deformation.
For example, PCB positioning and riveting, mechanical contact of test points during single board testing, etc. will cause deformation. In addition, semi-finished PCB boards cannot be directly stacked and so on.