The
Fuel Filters Assembly Manufacturers are companies that make fuel filters and other engine accessories. They offer replacement parts for cars, trucks and motorcycles. They also make filters for air compressors and vacuum pumps. These parts are available at auto-parts stores, but some companies sell them directly to consumers online. They also provide installation and maintenance services for engines, transmissions and differentials. Their products are used in cars, trucks and heavy equipment such as cranes, generators, lawn mowers and snow blowers.
The Company was founded in 1919. The Company has more than 30 product lines. They manufacture in accordance with OE requirements. They are a -tier supplier to major vehicle manufacturers worldwide. They have 13 large facilities in the US. They also export to over 100 countries around the world. They are partnered with Mopar and supply quality parts through local Chrysler dealers and repair shops. Their filtration systems are offered for both passenger cars and commercial vehicles.
Fuel Filter Water Separator is an important component of any diesel exhaust fluid (DEF) system. It removes urea crystals and other contaminants that may have been collected during storage. It also protects the DEF pump and injector from damage caused by corrosive contaminants that can contaminate the system.
Parker Hannifin Corporation is a global er in hydraulic, pneumatic and electromechanical filtration solutions. Its filter product lines include fuel, serviceable, disposable and drainage. Its filters are used in agricultural, automotive, aircraft, aerospace, marine, HVAC, military equipment, manufacturing, petroleum, refrigeration, transportation, medical and food industries. The Company has over 7,500 distributors serving greater than 350,000 customers worldwide.
A filter assembly consists of a plastic housing with an internal element that captures particles and contaminates. It also has a tube with a hose barb connector at one end and a metal mounting base. The hose barb connects to the fuel line, and the filter’s body rests on top of it.
In order to create a strong, leak-proof assembly, the components must be welded together with high-quality materials. Ultrasonic welding uses sound waves to melt and fuse the plastic, creating a stronger, more durable and longer-lasting assembly than traditional soldering or chemical bonding methods. The ultrasonic welding process also uses less heat, reducing the risk of cracking or warping. This type of assembly is especially useful for low-volume equipment manufacturers that design their own power systems rather than relying on off-the-shelf engines.
Another way to make a strong, leak-proof assembly is to use an injection molding technique. Injection molding involves melting and blending the plastic components to produce a solid part. This method is much faster than the traditional hand welding method. It is also a safer and cleaner method than using chemicals to assemble the plastic filter. In addition, this method of assembly can be used on a wide variety of plastics, including engineering plastics like PET and PCTg. These types of plastic are stronger, more durable and clearer than commodity plastics like PET and PETE.
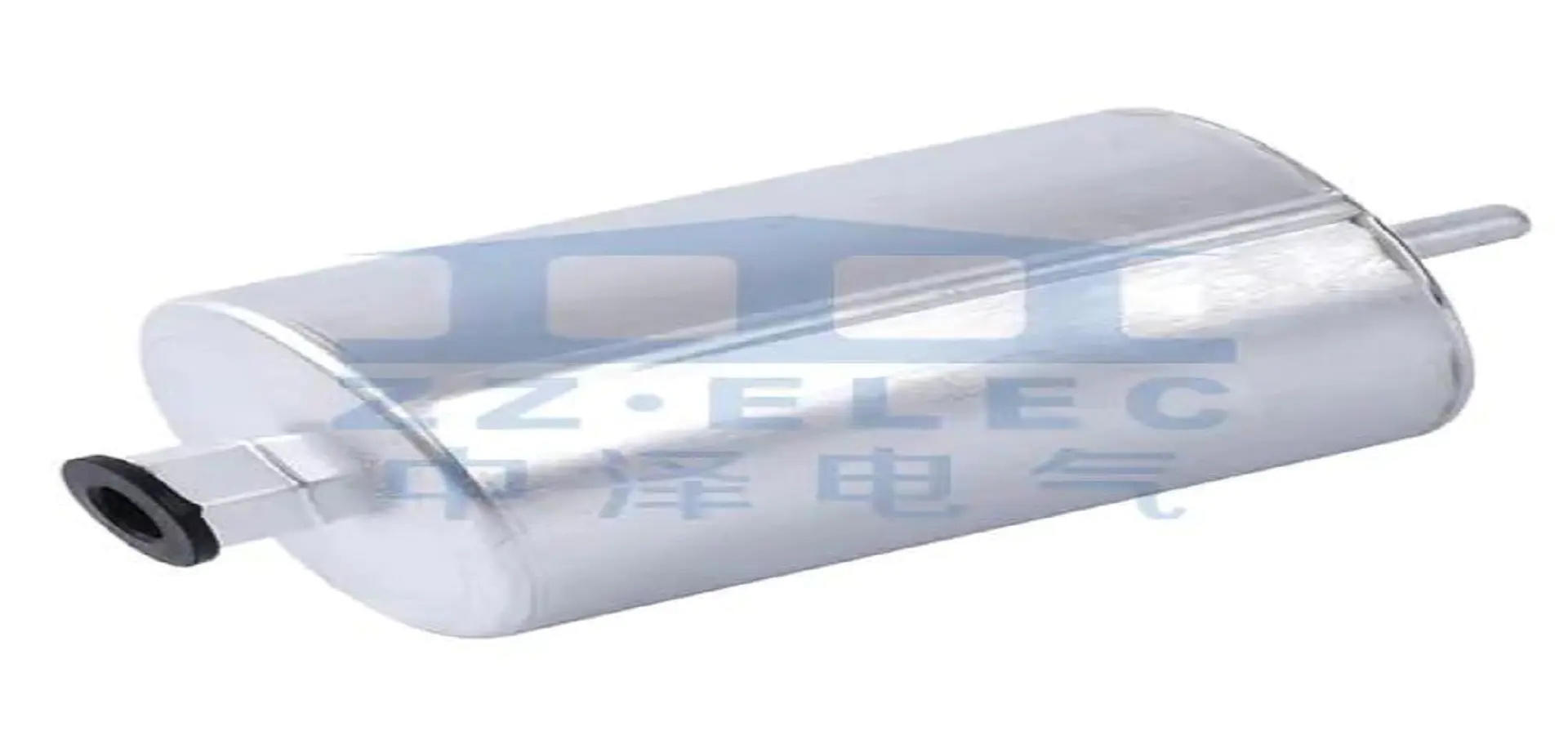